Advanced Applications of Strain Gages for Structural Health Monitoring
Micro-Measurements provides precision-engineered strain gages (gauges), instruments, and accessories designed to meet the demanding requirements of structural health monitoring. Engineers face increasing challenges in ensuring the safety, performance, and longevity of critical infrastructure and components, from bridges and pipelines to power generators and sports equipment. Our solutions deliver reliable, high-accuracy data for material testing, residual stress analysis, and real-time monitoring of structures, helping engineers identify potential issues before they escalate into costly failures. With Micro-Measurements, you gain the tools needed to monitor, test, and ensure the integrity of your projects.
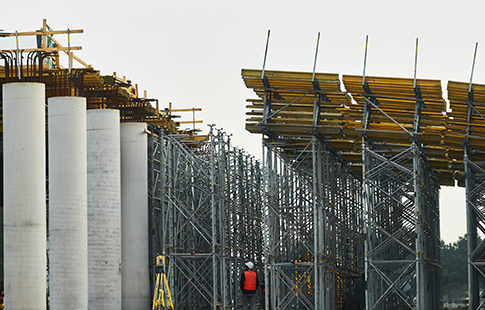
Core Features of Micro-Measurements' Structural Health Solutions:
- High-Precision Strain Measurement: Our strain gages (gauges) provide accurate, real-time data for monitoring the health of critical structures and components.
- Durable for Harsh Environments: Designed to perform in extreme conditions, our strain gages (gauges) withstand high temperatures, mechanical stress, and corrosion, ensuring long-term reliability.
- Seamless Data Acquisition: Our solutions integrate easily with modern data acquisition systems, enabling continuous, real-time monitoring of structural health.
- Customizable Solutions: Tailored configurations are available to meet the specific needs of diverse structural health monitoring applications.
- Early Detection of Structural Failures: With our precise strain measurement technology, potential issues such as material fatigue or stress buildup can be detected early, allowing for proactive maintenance and repair.
Industry-Specific Applications for Structural Health:
In the automotive industry, strain gages (gauges) are essential for monitoring structural components to ensure vehicle durability and performance. Testing laboratories rely on our sensors for material and endurance testing of critical car parts, allowing manufacturers to identify weaknesses and improve overall reliability.
In infrastructure, construction, and civil engineering, constant monitoring of structures like bridges, rail systems, and dams is crucial to prevent failures. Our strain gages (gauges) are integrated into these systems, providing real-time data on stress or strain to help detect potential issues early, reducing the risk of accidents and minimizing repair costs.
Across other industries, our strain gages (gauges) support safety and performance. In power generation and turbine manufacturing, they track stress and fatigue in turbine blades, aiding efficiency and reliability in energy production. Shipbuilders use them to monitor hull integrity, ensuring vessels can handle rough conditions. In geotechnical engineering, they measure residual stress in the ground and structures, providing crucial data for large-scale projects in complex environments. Additionally, in the sports and leisure industry, precision strain measurement supports the testing of equipment under repeated stress, ensuring durability and optimal performance for athletes and users.
INFRASTRUCTURE/CONSTRUCTION/CIVIL ENGINEERING
Micro-Measurements’ foil strain gages (gauges) are the most robust solution to monitor strain in concrete and metal structures. Our gages (gauges) are installed on structural components in bridges and buildings to measure stress and compare these measurements to analytical models and stress calculations.
POWER GENERATOR/TURBINE MANUFACTURES
Micro-Measurements’ strain gages (gauges) help detect equipment failure, malfunction, and unusual conditions found during regular operation or maintenance activities. Our sensing systems—including wireless and telemetry capabilities—accurately measure variables in pumps and other equipment that experience high thrust loads.
SHIP BUILDERS
Micro-Measurements’ strain gages (gauges) are used to measure the torque in ship parts such as fans, generators, wheels, or propellers in a motor, turbine, or engine. Our strain gages (gauges) are also used to measure and monitor mooring forces of ships. Common approaches include mounting a tension strain gage (gauge) load cells in line with mooring ropes or using a shear pin force strain gage (gauge) transducer.
FASTENER TESTING
Fasteners are ubiquitous in a variety of everyday structures, including infrastructure, equipment, and vehicles. These structures need to be safe and reliable. That’s why fasteners must perform to expectations and hold up to wear and tear such as stress, vibration, unexpected loads, and environmental conditions. Micro-Measurements’ metal foil strain gages (gauges) are key components in any fastener testing. These tests help to identify potential problems at an early stage, extend service life, and help reduce operating and replacement costs.
RESIDUAL STRESSES
An inevitable, and potentially costly, effect of the manufacturing and fabricating processes is residual stress. Most commonly, residual stresses are detrimental— contributing to fatigue and other structural failures that often go unrecognized until after a malfunction or failure occurs. The hole-drilling strain gage (gauge) method is a relatively simple procedure and has been standardized in ASTM Standard Test Method E 837. Learn more about the general theory of residual stress measurements in Micro-Measurements Tech Note TN-503, “Measurement of Residual Stresses by the Hole-Drilling Strain Gage Method”.
GEOTECHNICAL/GEOSCIENCE
Micro-Measurements’ strain gages (gauges) are expertly designed to meet unique challenges such as those found in constructions occurring on the earth’s surface or subsurface. Our gages (gauges) help determine mechanical properties for structures such as earth-filled dams, retaining walls, embankments, tunnels, dikes, and levees, channels, reservoirs, and landfills.
BRIDGES
Micro-Measurements’ foil strain gages (gauges) are used in bridge structures around the world to measure strain, displacement, force, temperature, inclination, bending movements, and alignment. A permanent installation provides long-term monitoring of the structure’s health, while a temporary installation ensures safe working conditions during a repair.
PIPELINES
Micro-Measurements’ metal foil strain gages (gauges) can be attached to various points along oil and gas pipelines to offer continuous, remote monitoring of the structures and help prevent threats to the flow inside the pipe as well as potential threats to the environment.
RAIL MONITORING
Micro-Measurements offers a wide range of strain gages (gauges) that provide long-term structural monitoring solutions for railways. The strain on rails, such as axial tension or compression, can and should be measured and monitored. Warnings enable maintenance, minimize impact on rail traffic, and ensure safety.
DAMS
Micro-Measurements’ impressive collection of strain gages (gauges) are well suited for monitoring and analyzing the behavior of a dam’s structural element. When strain gages (gauges) are used during the planning, design, construction, and operation of the dam, the performance of the dam’s structure is reliable and safe. In addition, our strain gages (gauges) are suitable to ascertain data related to other parts of the dam, such as the reservoir and river basin, to help ensure normal operation and safety.
MATERIAL & ENDURANCE TESTING
Precision, speed, and reliability are critical features in any force mechanism systems found in the metals processing industry. Metal foil gages (gauges) are used to determine how long an application can meet processing load demands. Measurements types include linear and shear force, torque, pressure, tension, and compression.
SPORT, LEISURE, & TRAINING EQUIPMENT
Micro-Measurements designs and manufactures hybrid sensors and strain gages (gauges), used in exercise and sports therapy equipment to monitor and/or control the level of effort exerted by the patient or to measure and track an athlete’s performance.
Ensure the safety and performance of your infrastructure and products with Micro-Measurements’ structural health monitoring solutions. Contact our sales team today to discuss how our precision strain gages and data acquisition systems can be customized for your specific needs, or visit our product catalog to learn more about our solutions for ensuring structural integrity across a wide range of industries.
Contact Our Structural Health Experts
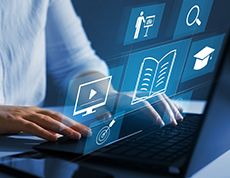
RESOURCES
Learn about our stress analysis products, watch informative videos, and explore our large knowledge base.
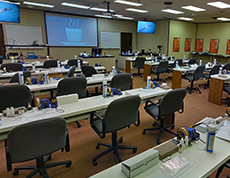
TRAINING
Benefit from an extensive series of regularly scheduled, hands-on technical workshops and short courses.
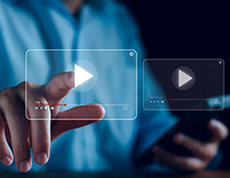
VIDEOS
Explore our extensive collection of tutorials and informational videos on a variety of strain measurement topics.
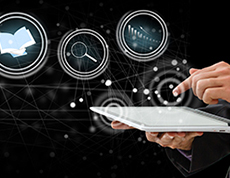
KNOWLEDGE BASE
Unlock a wealth of knowledge, from calculators to technical documents, to help you manage our strain gage (gauge) and PhotoStress® products.